Hard Anodizing Heat Exchangers
Over a number of years, Southwest United Industries in Tulsa, Oklahoma has successfully heated many process chemistries using Thermax2 heat exchangers driven by steam. But it was a troublesome cooling application that recently has brought United their greatest satisfaction with Thermax2 . Southwest was experiencing failures of 316L stainless steel coils in their 12% hard sulfuric anodizing process. Looking for another solution, Southwest asked its Process Technology
distributor, Electroplating Consultants, if Thermax2 could be used for cooling.
While Thermax2 is often used for cooling, it has not been recommended for cooling sulfuric acid. United was willing to take the risk. Southwest said that in the 15 months they have had the units in operation, they have been completely satisfied with the results.
In this case, Southwest plumbed five 7.8 ft2 Thermax2 units in parallel to support a flow rate of 130 gallons per minute. Its chilled water and glycol coolant mixture arrive at the exchanger at 22°F and the process chemistry is efficiently maintained at a steady 34°F.
When asked if the five units have trouble keeping up with the heat produced during anodizing, Southwest said they believe they could do the job with four of the Thermax2 exchangers, which allows them to replace a single unit without shutting down the process.
So far, there’s been no indication of any problems.
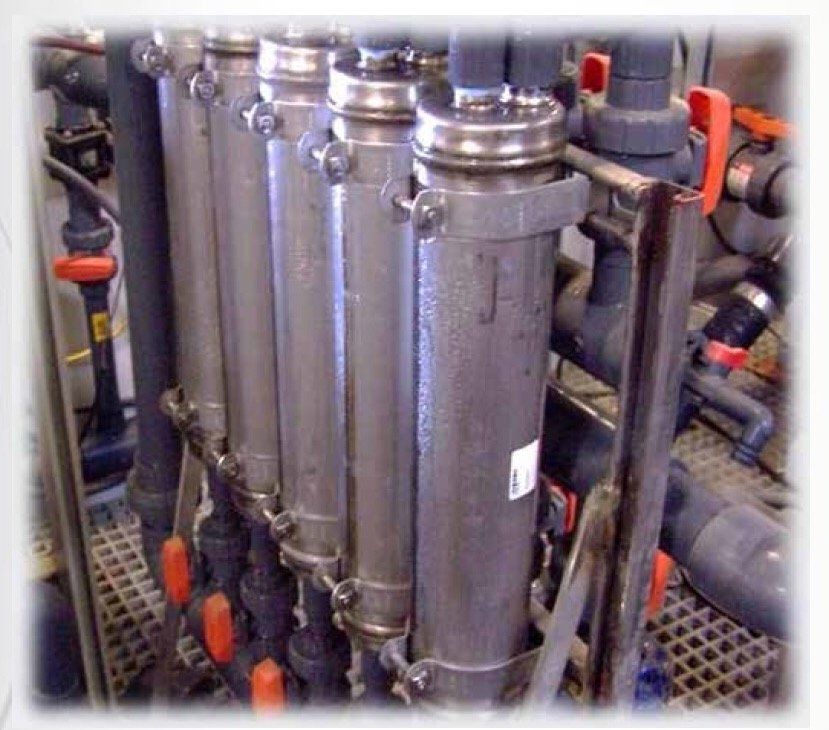
Thermax Heat Exchanger
Compared to a plate and frame ex-changer, the Thermax2 solution
was less than half the cost and had
no flow rate issues. Southwest
achieved full payback in about 3
months!
by Mark Emilio